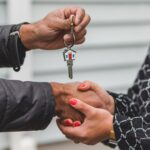
Unveiling Top Real Estate Market Trends
August 9, 2023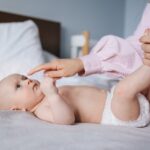
A Parent’s Guide to Baby Poop
August 12, 2023An effective introduction sets the stage and invites readers to enjoy the journey ahead. Furthermore, it should motivate them to keep reading further on.
Hand-cranked machines use metal dies similar to cookie cutters to cut and emboss material, particularly paper for cardmaking and scrapbooking projects.
Adjust the Height
A good cutting machine should enable its user to make subtle adjustments to cut height and speed as needed, especially for newcomers who wish to start with manufacturer recommendations before fine-tuning as they learn about its performance.
The Sizzix Big Shot Plus is an inexpensive, portable manual die cutter ideal for cutting paper, felt, cardstock, vinyl and stickers. Using metal dies pressed into materials under high pressure to cut it – and also embossing materials like rubber – this small and lightweight machine cuts paper, felt cardstock vinyl stickers with ease. Simply put a clear plate at the base of the machine; next add either no- or shim (depending on pressure needs); material; metal die (and second clear plate – repeat until cut!) and cut!
This manual cutter comes complete with a crank handle for effortless use without the use of a computer. Users have noted how simple and straightforward its operation and maintenance are, making this machine ideal for paper and cardstock, though other materials can also be handled successfully.
Adjusting cutting height requires loosening off both locking nuts on either side of the setting bar, then using height adjuster on both sides, lower or raise roller until it rests against bottom blade, then tighten all locking nuts accordingly. Repeat these steps on both sides. Once at correct height, tighten locking nuts securely – repeat this process on both machines! The turnbuckle on cutterbar can also be adjusted upward or downward so that operator can position cutterbar for optimal performance on every job; making these adjustments can directly influence how fast and accurately machine cuts cuts! This adjustment has direct implications on speed/accuracy ratio as it directly impacts performance on how fast/accurate machine cuts.
Adjust the Blade
Adjusted blades can make all the difference for clean, quality cuts. However, without knowing how to properly adjust them on your cutting machine it could result in poor finishes or costly repairs in the future.
To avoid such incidents, it’s essential to learn how to manually adjust a blade before each use and using appropriate tools for this task. Doing this ensures your adjustments are precise and secure while simultaneously keeping hands and fingers safe from potential injuries caused by coming too close to a blade.
Ideal, blade replacement should occur as soon as it shows signs of wear and tear to ensure smooth operation for longer. Inspecting blades regularly may also help detect any problems before they worsen.
Fabric type and how it’s being cut will also have an impact on the durability of your blades. For instance, using a cutter designed for other materials could put an excessive strain on its blade, leading to damage or injury of some sort.
Adjusting the blade of a commercial paper cutter regularly can extend its lifespan. Certain materials like coated stock, board and plastic material may quickly dull a blade compared to uncoated paper stocks or fine paper grades. You should replace damaged blades immediately as this can reduce quality cuts and may negatively affect their results.
Adjust the Pressure
Finding the right amount of pressure on the cutting machine you bought from the official cricut singapore store is vital to producing clean and accurate cuts. No matter if you are working with vinyl or another material, too much or too little pressure could ruin your project and even damage your machine if set incorrectly. Luckily, changing pressure levels is a straightforward process that can help you achieve amazing results for all of your projects.
First, ensure your blade is correctly installed into the machine. An ineffectively installed blade won’t cut through material correctly, leading to smudges or tears. In case it becomes dirty or worn down over time, remove it from its host machine and use an alcohol swab to clean it thoroughly.
If you’re cutting new material, try performing a test cut on some scrap to see how your settings perform on it and make any necessary adjustments. A similar practice should also be employed when switching materials or altering any part of your machine.
Keddell emphasizes the importance of connecting your machine correctly to an air source. Plasma machines require specific, dry air for proper operation; please refer to your owner manual to find out the optimal pressure and flow rates.
As soon as you select a material in your software, there should be a number associated with its name to indicate pressure settings for cutting it. While exact figures vary by cutter model, starting off low will help ensure you find an optimum setting that matches up with what material you’re cutting.
Adjust the Shims
Alternatively, if your project contains thin lines that could potentially get cut incorrectly by the blade or corners aren’t being cut properly, try out this feature of your cutter. When opening a file in it, click these icons order order, view direction> to set line order and view direction respectively; this will allow cuts to travel outward from geometry edges rather than toward them, while simultaneously helping prevent blade deformation or dragging on thin or acute angles.
Use the Reverse Direction tool from Tools to change the orientation of lines in the Cut Editor. With this selected, each time you click a line within the editor its direction will switch (indicated by a pink arrow at its starting point). This may help reduce instances where thin or acute features could catch and drag on thin blades – though it may not always be necessary depending on geometry considerations.
As well as an Adjust Shims function, this machine offers several other ways of helping you maintain straight lines. When working with small dies, for instance, adding shims at the bottom of your cutting mat can help create an even surface; you can also use tools like Align to ensure everything aligns properly; Push/Pull tools can control blade movement during cutting sessions.
One downside of this machine, however, is its limited advanced capabilities compared to other cutters. For example, it cannot make large cuts or work with thick materials as easily. Still, it makes an excellent option for beginners and hobbyists who wish to create greeting cards, custom labels or any other projects using different materials.
Clean the Blade
If you use one blade for all of your cutting tasks, it’s crucial that it stays clean regularly to avoid tape adhesive build-up and other residue that causes jamming of your cutter. Simple Green can easily do the trick here or citrus-based kitchen cleaners can work as they don’t emit harmful fumes; some even opt for oven cleaners but Freud advises against them since their chemicals could damage carbide tips as well as the binder that holds them together.
Once your blade has soaked for an appropriate period, use a wire brush or scraper to scrub it clean with some serious grit. After cleaning is complete, your blade should cut paper and vinyl more precisely than ever – some people even color code their blades so it’s easy for them to identify which one they are using when opening up their machine!
After you finish scrubbing, be sure to rinse your blade in clean water to flush away any residual cleaning solution and to help protect them from rusting and dulling quickly. Apply metal polish or rust inhibitor spray like WD-40 as soon as you reattach your blade; for optimal results apply before beginning work again so the cleaner or oil doesn’t start eating away at its surface; but you may apply as necessary throughout your project.